Das traut sich nicht jeder
Spezialaufträge gehören für die Elektro-Projekt Mittweida GmbH zum täglichen Geschäft. Eine Sonderanfertigung wie der Schaltschrankcontainer für die BSW begegnet Hubert Timmel trotzdem nicht jeden Tag.
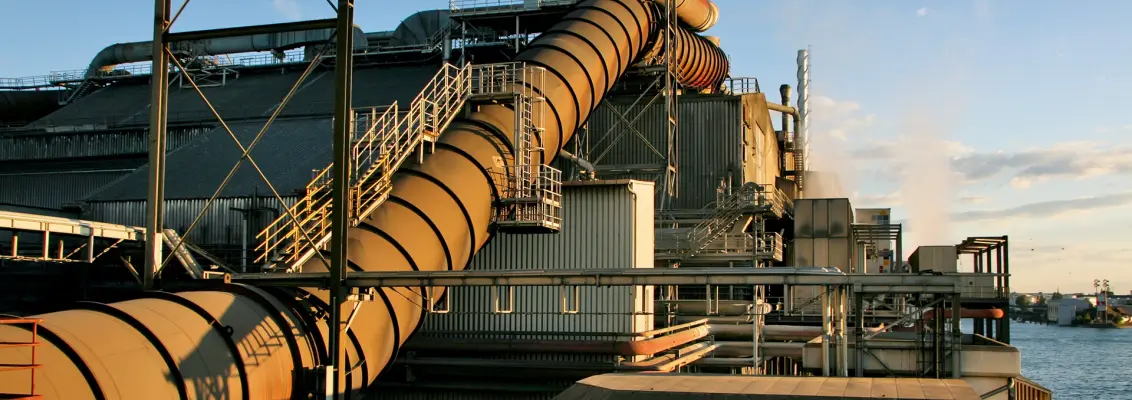
Drei Meter breit, drei Meter sechzig hoch und acht Meter lang ist der graue Container, dessen Weg in der Fertigungshalle der Elektro-Projekt Mittweida GmbH (EPM) im sächsischen Frankenberg begann und schon bald in Kehl am Rhein seinen finalen Ort finden soll. Der Geschäftsführer Hubert Timmel betritt den unscheinbaren Kasten durch eine der eingelassenen Türen. Mike Grambow, Gebietsverkaufsleiter bei HELUKABEL, folgt ihm. Er ist schon gespannt, wie die Kabel verbaut sind. „Häufig sehe ich das als Lieferant ja nicht. Jetzt kann ich auch mal wieder bei einem Testlauf live dabei sein.“ Sieben massive Metallschränke füllen die linke Containerhälfte – alle vollgestopft mit Steuerungstechnik. „Der Container ist für die Badische Stahlwerke GmbH (BSW) in Kehl. Er enthält den Mittelspannungsumrichter und die Steuerung für einen Entlüftungsventilator“, sagt Timmel und öffnet eine Schaltschranktür. Dahinter ein wohlgeordnetes Allerlei aus Kabeln, Steckverbindungen und Leiterplatten. Grambow erklärt, was zu sehen ist: „Neben Standardkabeln wie Mittelspannungskabel sind Servokabel verbaut, die den Ventilatormotor antreiben. Dieses Steuerkabel führt ins Freie und ist daher UV-beständig. Es verbindet die Containertechnik mit der Anlage im Stahlwerk. Und dann sind da noch die zahlreichen Einzeladern, die die Schaltschrankkomponenten verbinden.“
Gleich neben dem offenen Schaltschrank befindet sich das Herzstück der Anlage: ein Mittelspannungs-Frequenzumrichter. „Eine Spezialanfertigung, die wir gemeinsam mit Siemens entwickelt haben. Damit der Umrichter in den Container passt, haben wir um jeden Millimeter Baugröße gekämpft“, erklärt Timmel. Der Umrichter regelt die Drehzahl des Ventilators, der die Abgase der Schmelzöfen durch ein gigantisches Rohr von drei Meter Durchmesser bläst. „Bisher gab es nur zwei Zustände für den Ventilator: an oder aus. Das wollte die BSW ändern und gab den Auftrag zur Umrüstung.“ Die Technik von EPM wertet zukünftig Messdaten aus der Anlage aus und passt die Drehzahl an den tatsächlichen Bedarf an. „Die Mess- und Datenübertragungskabel sind dazu da, diese Informationen aus der Anlage an den eingebauten Rechner weiterzugeben“, erklärt Mike Grambow, während er auf die entsprechenden Kabelstränge zeigt. Hubert Timmel betont: „Die BSW kann so sehr viel Energie sparen!“
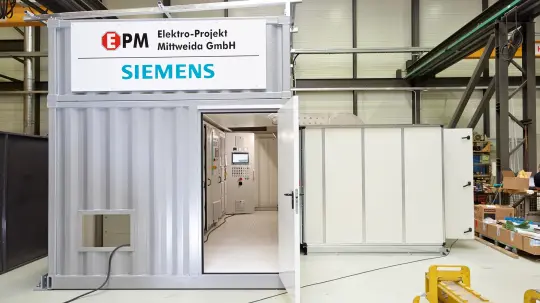
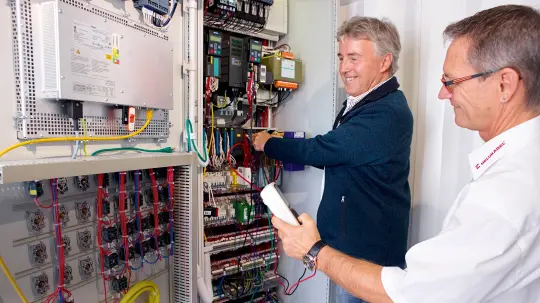
Ein besonderer Auftrag
Eigentlich sind Spezialanfertigungen wie diese nichts Besonderes für EPM, schließlich gehören außergewöhnliche Lösungen zum Geschäftsmodell des Unternehmens. „Wir machen Sachen, an die sich nicht jeder rantraut.“ Mit Sachen meint er Schaltanlagen- und Steuerschaltschränke für Kunden aus der Automobil- und Schwerindustrie sowie Hersteller von Sondermaschinen. „Wir verstehen uns als Komplettanbieter. Unser Leistungsspektrum reicht von der Hard- und Softwareplanung bis hin zur Lieferung und Inbetriebnahme.“ EPM ist damit sehr erfolgreich: Als Timmel mit der Firma Anfang der 90er-Jahre startete, beschäftigte er 16 Mitarbeiter, heute sind es schon 130. Der Auftrag für das badische Stahlwerk ist jedoch auch für Hubert Timmel kein gewöhnlicher. „Bei diesem Projekt muss einfach alles glattlaufen, sowohl technisch als auch terminlich.“ Denn so robust und gewaltig ein Stahlwerk auch scheinen mag, so sensibel reagiert es auf Störungen: Einfach abschalten geht nicht. Einmal abgekühlt, dauert es Tage, bis die Öfen wieder die Betriebstemperatur erreicht haben. Es musste also eine Lösung her, die den Betriebsablauf nicht stört. Aufwendige Umbauarbeiten vor Ort waren nicht möglich; daher kam nur eine schlüsselfertige Containerlösung infrage. „BSW hat uns für die Inbetriebnahme lediglich ein festes Zeitfenster von zwei Tagen gegeben.“ Um den Termin zu halten, brauchte Hubert Timmel also auch zuverlässige Lieferanten. Die EPM agiert für die BSW als Generalauftragnehmer; bis zu sechs verschiedene Unternehmen müssen sich daher eng verzahnt in den knappen Terminplan einreihen. „Mit HELUKABEL arbeiten wir schon seit vielen Jahren zusammen. Da wussten wir, dass wir uns auf eine pünktliche Lieferung verlassen können.“ Timmel und Grambow verlassen den Container. Die Generalprobe hat er bereits bestanden: Alle Funktionen wurden in den vergangenen Wochen in aufwendigen Tests mehrfach simuliert, Vertreter von der BSW haben die Technik bereits abgenommen. Jetzt muss er sich noch in der Praxis beweisen. „Morgen geht das Ding auf Reisen“, sagt Timmel und verabschiedet sich von Grambow. 550 Kilometer Strecke und zehn Stunden Fahrt auf einem Tieflader liegen vor dem Container.
Pünktliche Montage
Einen Tag später steht Timmel mit seinen vier mitgereisten Mitarbeitern um fünf Uhr in der Früh auf dem Gelände des Stahlwerks. Die meisten Menschen schlafen noch, doch Timmel und sein Trupp sind hellwach. Gespannt beobachten sie, wie der Kran den zwölf Tonnen schweren Container unter Anweisung von Timmel in 15 Meter Höhe behutsam auf dem vorgesehenen Podest absetzt. Vor der imposanten Kulisse des Stahlwerks wirkt er wie ein Bauklötzchen. „Die erste Hürde ist schon mal genommen“, sagt Timmel und macht sich zusammen mit seinen Mitarbeitern gleich an die Arbeit. Am Ende des zweiten Montagetags atmen alle auf: Sie haben es geschafft, die Technik arbeitet reibungslos. Sollte doch mal eine Komponente ausfallen, ist schon vorgesorgt: „Das Dach des Containers, auch Top genannt, lässt sich einfach abnehmen, ohne dass ein Leistungs- oder Steuerkabel abgeklemmt werden muss. Größere Teile kann man so auch während des Betriebs austauschen, ohne größere Stillstandszeiten zu produzieren.“