Im Takt der Montagelinie
Ohne das intensive Zusammenspiel mit dem Kabelkonfektionär Eisele Elektronik GmbH würden Montage und Verkabelung der Maschinen und Anlagen im Werk Schopfloch der HOMAG Group nicht so reibungslos funktionieren. Verbaut werden Kabel und Leitungen von HELUKABEL.
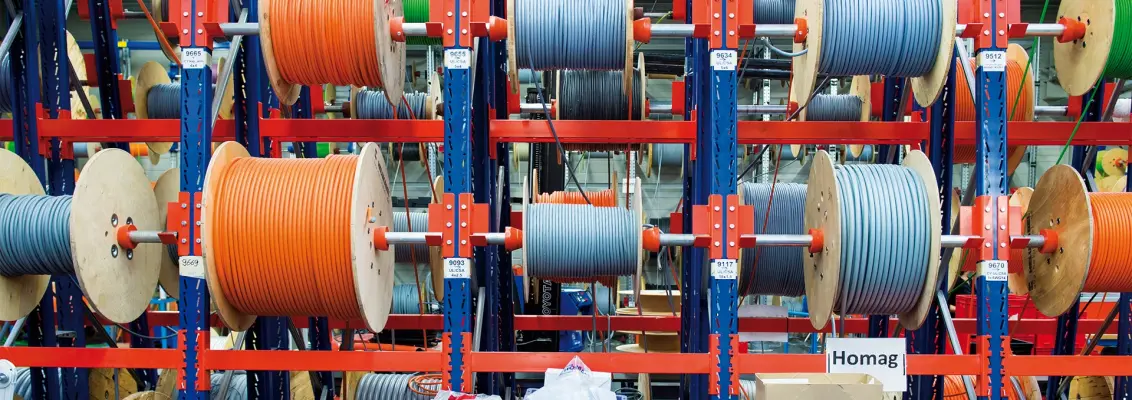
Rainer Maier ist seit zwei Jahrzehnten der Mann von HELUKABEL für die HOMAG Group. Er erinnert sich schmunzelnd, wie er einst die Frage „Können Sie auch Kanban?“ mit einem deutlichen „Ja“ beantwortet hatte – um anschließend zu Hause nachzuschlagen, was denn Kanban überhaupt bedeutet. Heute ist er Experte. Kanban beschreibt das Prinzip der Lieferung von Teilen und Baugruppen direkt in den Takt der Fertigung – just in time. Das ist bis heute eines der Erfolgsrezepte der HOMAG Group, des weltweit führenden Anbieters von Maschinen für die Holzbearbeitung. Das Just-in-time-Prinzip gilt auch für die aufwendige Verkabelung der HOMAG-Maschinen am Standort Schopfloch. Im gesamten Werk findet man nur eine Handvoll in der Ecke platzierter Kabelrollen. Alle anderen Kabel kommen vom Zulieferer minutengenau, direkt im Fertigungstakt an die Linie. Das leistet die nur knapp vier Kilometer entfernte Eisele Elektronik GmbH. Deren Team stellt ganz individuell für jedes Bearbeitungszentrum und jede Durchlaufmaschine Kabelsätze und elektrische Baugruppen bereit.
Erste Berührungspunkte zwischen der HOMAG Group, HELUKABEL und Eisele gab es schon Anfang der 1990er-Jahre, intensiver wurde die Zusammenarbeit ab 1996. Immer kürzere Taktzyklen an der Holzbearbeitungsmaschine von HOMAG und damit eine deutlich höhere Dynamik verlangten viel von den verbauten Kabeln. Rainer Maier, der zuständige Kundenbetreuer bei HELUKABEL, wurde schnell zum Berater seines Schlüsselkunden. Dem empfahl er angesichts der immer schnelleren Maschinenbewegungen, die PVC-Kabel durch die PUR-Variante in der Schleppkette zu ersetzen. Maier: „Die vorher in den Prototypen verwendeten PVC-Flachkabel verendeten im Versuchslauf wie die Mücken im Kerzenlicht.“ Der Wechsel auf PUR-Kabel zahlte sich aus. Bis heute wurde bei keiner einzigen Maschine aus dem Stammwerk der HOMAG Group in Schopfloch ein Leitungsausfall als Störgrund gemeldet, und das bei – über alle Maschinen hochgerechnet – rund 60 Millionen absolvierten Doppelbiegezyklen.
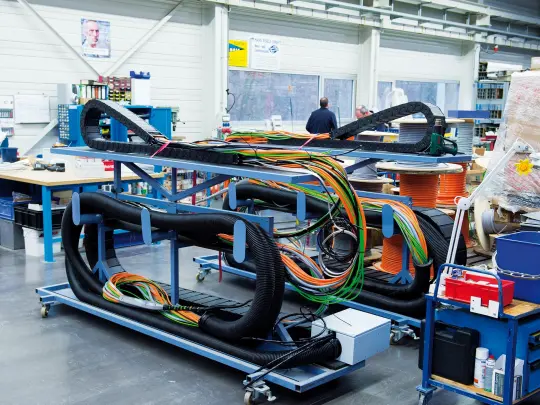
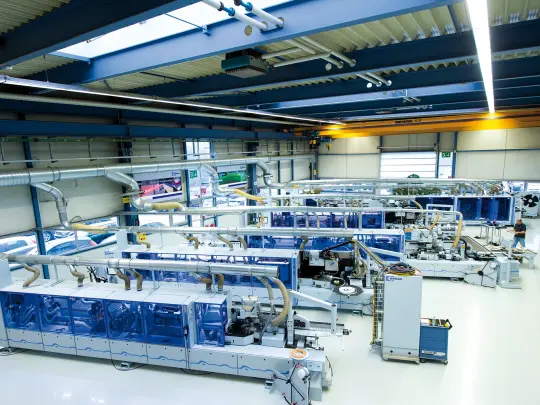
Nah am Kunden
Der gelernte Elektromeister Maier ist im Wochentakt in Schopfloch vor Ort und ist telefonisch rund um die Uhr erreichbar. Nicht nur, um gemeinsam über neue Bedarfe zu reden, sondern auch, um Schulungen abzuhalten. Schließlich ist die richtige Kabelführung nicht nur ein wichtiges Qualitätsmerkmal von Topmaschinen, sondern auch ein Faktor für Langlebigkeit. Bernd Bok, Leiter Strategischer Einkauf der HOMAG Group, betont: „Die gesamte HOMAG Group kann mit HELUKABEL auf einen erfahrenen Sparringspartner zugreifen.“ Der war 1999 auch gefragt, als das Werk Schopfloch seine Wertschöpfungskette auf den Prüfstand stellte und sich Rainer Maier zu Kanban bekannte. Angelehnt an die japanische Fertigungsmethode wollte der Maschinen- und Anlagenhersteller Abläufe verschlanken und Prozesse optimieren. Schließlich sollten auch weiterhin immer komplexere Maschinen mit zunehmend höherem Automatisierungsgrad rationell gefertigt werden. Die HOMAG Group wollte sich im Zuge dieser Überlegungen auf ihre Kernkompetenzen fokussieren – das Zusammenführen aller Komponenten in der Montage und die Inbetriebnahme des Gesamtsystems beim Kunden. In diesem Zusammenhang drängte sich auch die Verlagerung der Kabelkonfektionierung zu einem Dienstleister auf, verbunden mit einer taktgenauen Anlieferung in die Montage. Die Entscheidung fiel am Standort Schopfloch zugunsten der Eisele Elektronik GmbH.
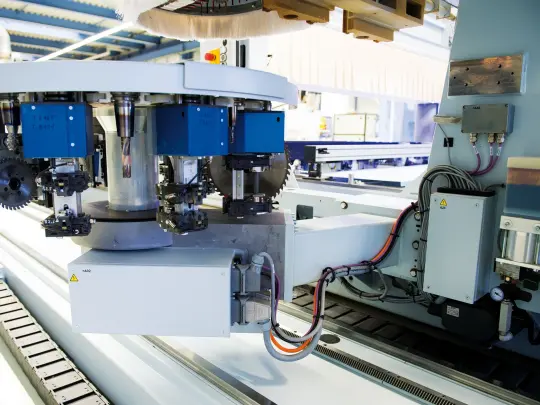
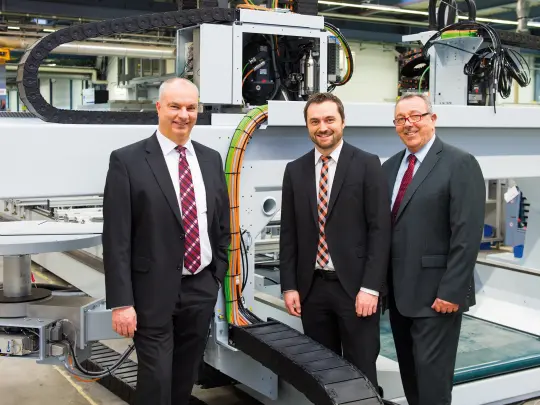
Konfektionär mit Ideen
Dr. Sebastian Eisele investierte im Laufe der Zusammenarbeit einiges, um mit den Anforderungen aus Schopfloch Schritt zu halten. Die Verwendung von konfektionierten Kabelbäumen nach dem Vorbild der Automobilindustrie reduziert die Verdrahtungsarbeit am Schaltschrank drastisch. „Bei manchen Schränken sinkt der Aufwand um über 70 Prozent“, strahlt Ingenieur Eisele. Im Zentrum der Kabelbaumfertigung steht eine Maschine, die vollautomatisch Kabel ablängt, die Enden beidseitig abisoliert, die Litzen im Ultraschallverfahren verschweißt, alle Schweißpunkte vollautomatisch prüft und die Kabel schlussendlich spezifisch beschriftet. Bei der Umsetzung der maschinenindividuellen Vorkonfektionierung war auch die Flexibilität von HELUKABEL gefragt. Denn die hauseigene Beschriftung der Kabel überlagerte sich immer wieder mit der typenspezifischen Beschriftung im Vollautomaten. Deshalb bekommt der Konfektionär jetzt alle Kabelvarianten mit einer Herstellerprägung, die der Beschriftung nicht in die Quere kommt. Der Vollautomat wurde so erweitert, dass statt nur zehn Meter jetzt auch bis zu 25 Meter lange Drahtsätze verarbeitet werden können. Damit wird für jede Maschine vom Werk Schopfloch ein Großteil des kompletten Kabelsatzes vorkonfektioniert, der Rest bleibt Handarbeit. Dieses Vorgehen sei nicht nur ein wichtiger Schritt hin zu mehr Montagefreundlichkeit, betont Sebastian Eisele: „Für das Werk Schopfloch der HOMAG Group war vorher die Maschinenverdrahtung ein großer Kostenblock. Mit der vorkonfektionierten Kabelanlieferung spart unser Kunde heute eine Menge Geld.“ Die Tüftler bei Eisele punkten auch mit frischen Ideen. Beispielsweise konstruierten Sebastian Eisele und sein Team zusammen mit dem Kunden Transportwagen für Schleppketten, Schaltschränke und elektrische Baugruppen. Ketten oder vorverkabelte Baugruppen lagern exakt auf Höhe des Maschinentisches der jeweiligen Zielanlage. So können die Monteure im Schopflocher Werk der HOMAG Group ohne großen Kraftaufwand das Ensemble einfach in die Maschine schieben.
Höchste Verfügbarkeit
Sebastian Eisele: „Wir sind voll in das System des Kunden eingebunden. Um Ruhe in den Abläufen zu bewahren und gegebenenfalls schnell auf Planumstellungen reagieren zu können, arbeiten wir immer zwei Takte im Voraus.“ Das Schnittstellenprogramm zur Übernahme der Daten aus der HOMAG-Montageplanung wurde bei Eisele programmiert. Dabei trägt die Eisele GmbH die Verantwortung für hundertprozentige Kabelverfügbarkeit. Sebastian Eisele: „Angesichts der engen Terminfenster spielt auch die räumliche Nähe eine wichtige Rolle.“ Die Pünktlichkeit überzeugte übrigens auch einstige Skeptiker im Service der HOMAG Group. Alle Kabel, die bis 14 Uhr bei Eisele bestellt werden, sind noch am gleichen Tag am Bedarfsort.
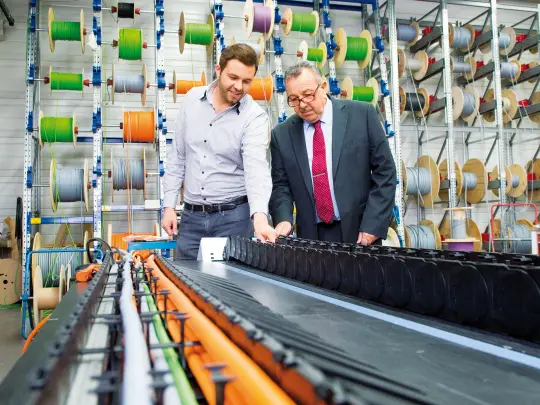
Im Zeichen von Industrie 4.0
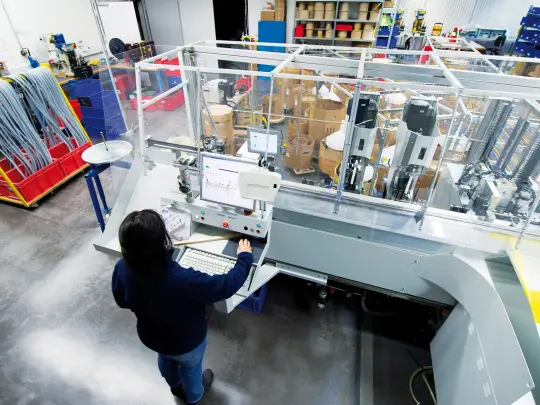
Gemeinsam mit der HOMAG Group und HELUKABEL steht Eisele jetzt vor neuen Herausforderungen. Schließlich, meint Bernd Bok, bedeute das Thema Industrie 4.0 eine riesige Chance: „Robotik und die zunehmende Vernetzung aller Komponenten in der Fabrik sind die Zukunft und wir sehen uns dabei als Vorreiter unserer Branche.“ Das birgt Potenzial für Produkte von HELUKABEL wie Roboterkabel, Hybridlösungen und Ethernetleitungen. Und weil die Dynamik der Maschinen bei weitem nicht ausgereizt ist, werden für immer höheres Tempo immer standfestere Kabelvarianten gebraucht. HELUKABEL ist zudem geografisch gefordert, da die HOMAG Group sich zunehmend globaler aufstellt. So erfolgt beispielsweise die Schaltschrankfertigung künftig im polnischen Werk.
Bernd Bok ist zuversichtlich. Schließlich haben HELUKABEL und Eisele in der Vergangenheit bewiesen, dass auf sie Verlass ist. Das wurde von der HOMAG Group auch ausdrücklich anerkannt. Über alle Warengruppen hinweg kürt der weltweit führende Anbieter von Maschinen für die Holzbearbeitung jährlich seinen Toplieferanten. Einziger Doppelsieger in 20 Jahren bei der Wahl des „Lieferanten des Jahres“ ist HELUKABEL. Zudem erhielt 2011 Eisele den begehrten Titel. Es sei kein Zufall, meint Bernd Bok, dass das Thema „Kabel“ dreimal den Preis bestimmte: „Kabel sind für mich die Adern unserer Maschinen und Anlagen. Mit HELUKABEL und Eisele Elektronik haben wir Lieferanten ausgezeichnet, mit denen uns seit Jahrzehnten eine intensive Partnerschaft verbindet und die mit exzellenter Qualität und absoluter Termintreue punkten.“
Die HOMAG Group AG ist der weltweit führende Hersteller von Maschinen und Anlagen für die Holz bearbeitende Industrie und das Handwerk. Das zum Dürr-Konzern gehörende Unternehmen beschäftigt etwa 6.000 Mitarbeiter und erwartet für 2015 rund eine Milliarde Euro Konzernumsatz. Mit 23 eigenen Vertriebs- und Servicegesellschaften sowie 15 Produktionsstandorten rund um den Globus gilt die HOMAG Group als Global Player.
Die Eisele Elektronik GmbH hat sich vom Kabelkonfektionär zum Systemzulieferer für den Maschinenbau entwickelt. Neben der HOMAG Group zählen namhafte Unternehmen wie Arburg und L’Orange zum Kundenkreis. Die Schwestergesellschaft Hans Eisele GmbH ergänzt das Angebot als klassischer Elektroinstallationsbetrieb für Büro- und Fabrikgebäude. Über 100 Mitarbeiter sind am Stammsitz in Glatten beschäftigt.